
Installation of non-destructive testing of pump-compressor tubes
Installation of non-destructive testing (flaw detection) of pump-compressis pipes (hereinafter referred to as the Installation of flaw detection) is intended for carrying out non-destructive testing (flaw detection) of the body material of new or repaired pump-compressor pipes in order to detect unacceptable defects.
Description
Installation of non-destructive testing (flaw detection) of pump-compressis pipes (hereinafter referred to as the Installation of flaw detection) is intended for carrying out non-destructive testing (flaw detection) of the body material of new or repaired pump-compressor pipes in order to detect unacceptable defects. Both pipes with a screwed coupling and pipes without a coupling can be controlled.
Installation of flaw detection is installed in the existing production line of the workshop, or installed in a separate production line.
The physical principle of operation of the flaw detection unit is based on the formation of a magnetic field in the pipe material with the help of a magnetic system and the subsequent recording of changes in a number of parameters of this magnetic field by integral sensors.
Installation kit:
Key features and benefits:
Installation of flaw detection is installed in the existing production line of the workshop, or installed in a separate production line.
The physical principle of operation of the flaw detection unit is based on the formation of a magnetic field in the pipe material with the help of a magnetic system and the subsequent recording of changes in a number of parameters of this magnetic field by integral sensors.
Installation kit:
- Receiving frame – 1 pc.
- Flaw detector section - 5 pcs.
- Drive mechanism (DM) - 2 pcs.
- Broaching mechanism single (BM) - 1 pc.
Key features and benefits:
- Resistance to the presence of scale, corrosion, traces of dirt and oil products on the surface of the pipe.
- The design of the scanning device (sensor unit) eliminates the destruction of the sensors when inspecting pipes that have tearing on the surface and tearing out metal.
- Modular design of sensor units.
- Low power consumption.
- No demagnetization of the pipe after fault detection.
- Availability of the system of self-testing and testing the operability of sensors operating in the continuous monitoring mode with the issuance of diagnostic results.
- Easy to maintain and repair. It is enough to replace the sensor units for another pipe size or replace the failed ones.
Photo
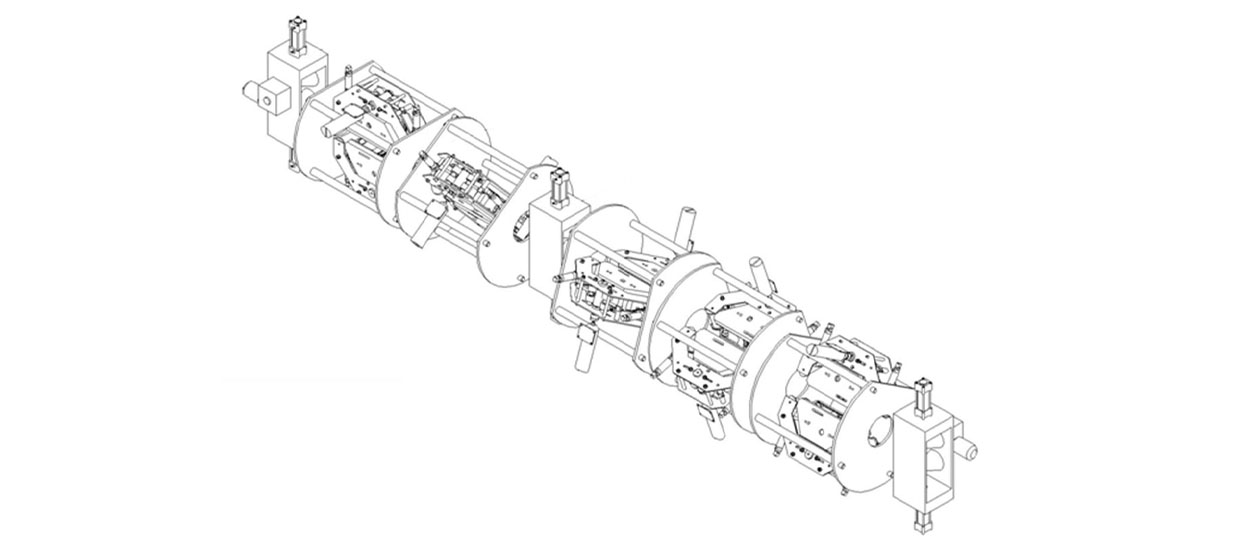
Video
Installation of non-destructive testing (flaw detection) of pump-compressis pipes (hereinafter referred to as the Installation of flaw detection) is intended for carrying out non-destructive testing (flaw detection) of the body material of new or repaired pump-compressor pipes in order to detect unacceptable defects. Both pipes with a screwed coupling and pipes without a coupling can be controlled.
Installation of flaw detection is installed in the existing production line of the workshop, or installed in a separate production line.
The physical principle of operation of the flaw detection unit is based on the formation of a magnetic field in the pipe material with the help of a magnetic system and the subsequent recording of changes in a number of parameters of this magnetic field by integral sensors.
Installation kit:
Key features and benefits:
Installation of flaw detection is installed in the existing production line of the workshop, or installed in a separate production line.
The physical principle of operation of the flaw detection unit is based on the formation of a magnetic field in the pipe material with the help of a magnetic system and the subsequent recording of changes in a number of parameters of this magnetic field by integral sensors.
Installation kit:
- Receiving frame – 1 pc.
- Flaw detector section - 5 pcs.
- Drive mechanism (DM) - 2 pcs.
- Broaching mechanism single (BM) - 1 pc.
Key features and benefits:
- Resistance to the presence of scale, corrosion, traces of dirt and oil products on the surface of the pipe.
- The design of the scanning device (sensor unit) eliminates the destruction of the sensors when inspecting pipes that have tearing on the surface and tearing out metal.
- Modular design of sensor units.
- Low power consumption.
- No demagnetization of the pipe after fault detection.
- Availability of the system of self-testing and testing the operability of sensors operating in the continuous monitoring mode with the issuance of diagnostic results.
- Easy to maintain and repair. It is enough to replace the sensor units for another pipe size or replace the failed ones.
Contacts
Central office and factory:
Tel./Fax: +7 (3812) 36 74 02, 36 74 12, 36 78 54, 48 48 30
e-mail: info@policon-rt.ru
Moscow office:
66 Leningradskiy prospekt, Moscow, 125315, Russia
Tel: +7 (499) 649 60 10, +7 (915) 198 09 21
e-mail: dech@policon-rt.ru
66 Leningradskiy prospekt, Moscow, 125315, Russia
Tel: +7 (499) 649 60 10, +7 (915) 198 09 21
e-mail: dech@policon-rt.ru
Yekaterinburg office:
80 Komsomolskaya Str, Yekaterinburg, 620138, Russia
Tel./Fax: +7 (343) 272 82 78, +7 (982) 630 25 15
e-mail: ural@policon-rt.ru
Contacts
Central office and factory:
Tel./Fax: +7 (3812) 36 74 02, 36 74 12, 36 78 54, 48 48 30
e-mail: info@policon-rt.ru
Moscow office:
66 Leningradskiy prospekt, Moscow, 125315, Russia
Tel: +7 (499) 649 60 10, +7 (915) 198 09 21
e-mail: dech@policon-rt.ru
66 Leningradskiy prospekt, Moscow, 125315, Russia
Tel: +7 (499) 649 60 10, +7 (915) 198 09 21
e-mail: dech@policon-rt.ru
Yekaterinburg office:
80 Komsomolskaya Str, Yekaterinburg, 620138, Russia
Tel./Fax: +7 (343) 272 82 78, +7 (982) 630 25 15
e-mail: ural@policon-rt.ru